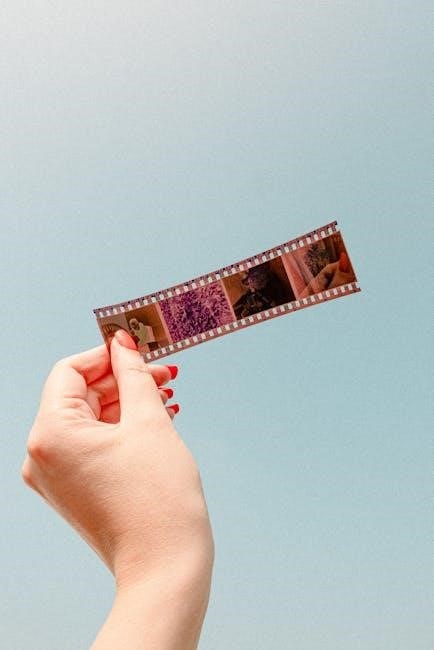
bomba manual
What is a Manual Pump?
A manual pump is a hydraulic device leveraging human power and mechanical advantage to displace fluids or air. These pumps, used globally, are fundamental for moving liquids from wells or containers, suitable for diverse applications like water extraction and more.
What is a Manual Pump?
Definition and Basic Principle
A manual pump operates by converting manual force into fluid motion, primarily used for extracting water or transferring liquids. Its basic principle involves creating a vacuum that draws fluid into a chamber, followed by displacing the fluid through an outlet using human-powered action. Typically, this action is achieved via a handle or lever that drives a piston or diaphragm. The mechanical advantage allows users to pump liquids from depths or containers with relative ease. Essential components include a cylinder, piston, valves, and an operating handle. These pumps are widely employed in areas lacking electrical infrastructure for water supply, irrigation, and industrial applications.
Types of Manual Pumps
Manual pumps come in several designs, including piston, diaphragm, and rotary vane models. Each type utilizes a unique mechanism to move fluids, catering to different needs and applications across various industries.
Piston Pumps
Piston pumps are a type of manual pump that operates using a reciprocating piston to create suction and pressure, effectively moving fluids. These pumps typically consist of a cylinder, a piston, valves, and an operating lever or handle. The piston’s back-and-forth motion within the cylinder creates a vacuum, drawing fluid into the chamber. As the piston moves forward, it forces the fluid out through a discharge valve.
Commonly found in hand-operated water pumps, piston pumps are valued for their simple design and ability to generate high pressure. They are often used in situations where electricity is not available or practical, such as in rural areas for drawing water from wells. The manual operation requires physical effort, but the robust construction and reliable performance make piston pumps a dependable choice for many applications.
Diaphragm Pumps
Diaphragm pumps, another type of manual pump, utilize a flexible diaphragm to displace fluid. These pumps work through the reciprocating motion of a diaphragm, typically made of rubber or another flexible material, creating alternating suction and pressure within a chamber. As the diaphragm moves in one direction, it increases the chamber volume, drawing fluid in through an inlet valve.
When the diaphragm moves in the opposite direction, it decreases the chamber volume, forcing the fluid out through a discharge valve. Diaphragm pumps are valued for their ability to handle fluids with solid particles and their resistance to corrosion. They are commonly used in applications such as transferring chemicals, pumping sludge, and in situations where maintaining fluid purity is essential. The manual operation involves moving a lever connected to the diaphragm, providing a simple yet effective pumping mechanism.
Rotary Vane Pumps
Rotary vane pumps represent another distinct category of manual pumps, employing a rotating rotor with vanes that slide in and out to create chambers for fluid displacement. As the rotor turns within the pump housing, the vanes trap fluid and carry it from the inlet to the outlet port. The sliding action of the vanes ensures a tight seal against the pump housing, maintaining consistent pressure and flow.
Manually operated rotary vane pumps often feature a handle or crank that turns the rotor, providing a direct and controllable pumping action. These pumps are well-suited for applications requiring a steady flow rate and are commonly used for transferring oils, fuels, and other viscous liquids. Their design allows for efficient pumping with minimal pulsation, making them a reliable choice for various manual fluid transfer needs.
Applications of Manual Pumps
Manual pumps are indispensable for water extraction, especially in rural areas. They efficiently draw water from wells, providing potable water and enabling irrigation, offering a reliable solution where electricity is scarce or unavailable.
Water Extraction
Manual pumps are widely used for water extraction, particularly in regions where electricity is limited or unavailable. Their primary function involves drawing water from sources like wells, boreholes, and shallow reservoirs, providing essential access to potable water for drinking, cooking, and sanitation purposes. These pumps are invaluable in rural communities and developing countries, where they serve as a lifeline for accessing clean water.
Furthermore, manual pumps are employed in agricultural settings for irrigation purposes, enabling farmers to cultivate crops even in areas with limited rainfall. Their simplicity and independence from external power sources make them a sustainable solution for water management. The ease of operation and maintenance further contributes to their popularity among communities relying on self-sufficient water solutions. They represent a reliable and affordable means of securing water resources.
Industrial Use
In various industrial settings, manual pumps play a crucial role in fluid transfer and handling processes. They are utilized for dispensing chemicals, oils, and other liquids from drums or containers, offering a controlled and precise method for transferring fluids between vessels. Manual pumps are particularly valuable in situations where electricity is unavailable or where the risk of electrical hazards necessitates non-electrical equipment.
Furthermore, manual pumps are employed in laboratories and research facilities for precise liquid dispensing and sampling. Their ability to handle a wide range of fluids, including corrosive or hazardous substances, makes them indispensable tools for scientific applications. The portability and ease of use of manual pumps also contribute to their popularity in field operations and remote industrial sites. They ensure safe and efficient fluid management in diverse industrial environments.
Marine Applications
Manual pumps find vital applications in marine environments due to their reliability and independence from electrical power. They are commonly used for bilge pumping, removing accumulated water from the hull of a boat, ensuring buoyancy and preventing potential damage. In sailboats and smaller vessels, manual pumps serve as essential backups in case of electrical system failures, providing a means to dewater the boat and maintain stability.
Additionally, manual pumps are employed for transferring fuel or water on board, especially in situations where access to electric pumps is limited or impractical. Their simplicity and durability make them ideal for the harsh marine conditions, where saltwater exposure and constant motion can compromise electrical equipment. Manual pumps offer a dependable solution for fluid management in various marine scenarios.
Safety Considerations for Using Manual Pumps
Using manual pumps safely requires understanding potential hazards. Always consult the manufacturer’s manual. When handling flammable fluids, take precautions to mitigate fire risks and ensure safe operation and prevent accidents.
Reading the Manufacturer’s Manual
Prioritizing safety when operating any manual pump starts with thoroughly reviewing the manufacturer’s manual. This document contains critical information regarding the pump’s specific operation, maintenance, and safety precautions. Understanding the recommended usage guidelines is paramount for preventing accidents and ensuring the pump’s longevity.
The manual will detail the types of fluids the pump is designed to handle, pressure limits, and any specific risks associated with its use. It also outlines the correct procedures for installation, priming, and routine maintenance, which are crucial for safe and efficient operation.
Ignoring these instructions can lead to pump malfunction, personal injury, or environmental damage. Therefore, taking the time to read and understand the manual is an essential step in ensuring safe operation.
Risks Associated with Flammable Fluids
Operating manual pumps with flammable fluids introduces significant safety hazards. These fluids, such as gasoline, solvents, and certain chemicals, pose fire and explosion risks if not handled with extreme caution. A static discharge generated during pumping can ignite flammable vapors, leading to a rapid and dangerous fire.
It is essential to ensure proper grounding and ventilation when working with these liquids. Avoid any sources of ignition, such as open flames, sparks, or lit cigarettes, in the vicinity. Use only pumps specifically designed and rated for flammable fluids, and ensure they are in good working condition.
Always wear appropriate personal protective equipment, including gloves and eye protection, to prevent skin contact and potential injury. Understanding and mitigating these risks is crucial for maintaining a safe working environment.
Advantages and Disadvantages of Manual Pumps
Manual pumps offer simplicity and independence from external power. They are mechanically simple, reliable, and functional in areas without electricity, proving invaluable in remote locations or during emergencies, making them versatile tools.
Advantages: Simplicity and Independence from Power Sources
Manual pumps boast several key advantages, most notably their simplicity in design and operation. Requiring no electricity or fuel, these pumps offer a reliable solution where power sources are unavailable or unreliable. This independence makes them indispensable in rural areas, developing countries, and emergency situations where access to power is limited.
Their straightforward mechanics minimize potential points of failure, contributing to durability and ease of maintenance. The absence of complex components translates to lower repair costs and reduces the reliance on specialized technicians. Furthermore, the manual operation allows for precise control over the pumping process, enabling users to adjust the flow rate as needed. Manual pumps are beneficial for various applications due to their simplicity.
Disadvantages: Physical Effort and Maintenance
Despite their advantages, manual pumps have limitations, primarily the physical effort required for operation. Pumping water or other fluids manually can be strenuous, especially for extended periods or with high volumes. This can be a significant drawback in situations where large quantities of fluid need to be moved or where the user’s physical strength is limited.
Maintenance is another consideration. While manual pumps are generally durable, they require regular upkeep to ensure optimal performance. This includes lubricating moving parts, replacing worn seals, and inspecting for corrosion or damage. Neglecting maintenance can lead to decreased efficiency, increased effort, and potential pump failure. The need for physical exertion and continuous maintenance reduces manual pump efficiency.